How to process parcel batches?
When multiple outbound orders need to processed, a parcel batch can be created to perform batch picking, packing, and shipping on outbound orders.
1. Create a batch
Steps: Outbound management> Parcel Outbound order>To Pick> Choose outbound orders to be included in the batch > Click drop down for Manage Batch> Create Batch
Add to Batch: add order to existing parcel batch order.
Create Batch: Create a new parcel batch order.
After the batch order is successfully created, ait will show in the “Processing” state under the Parcel Batches module. Click Pick to enter the batch picking page, or click Print Picking List to view the outbound list in the entire batch.
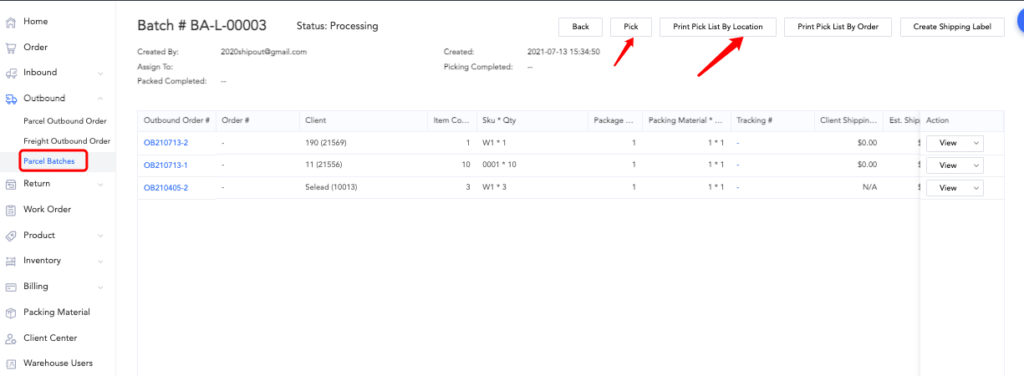
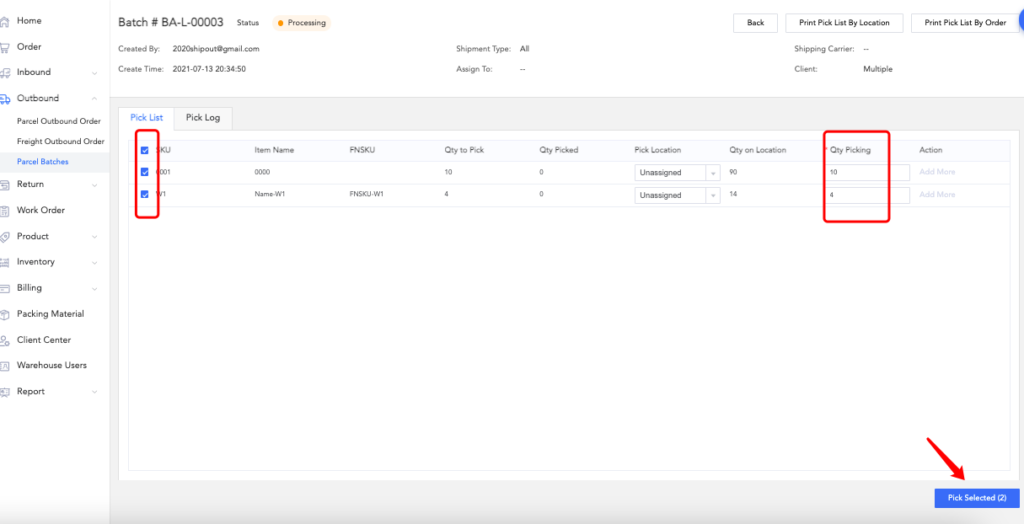
After batch picking is completed, go to “to pack” > find the corresponding batch number > click on packaging > enter the batch packaging interface;
Note: If the shipping label has already been issued, please return to the parcel outbound order module’s “to pack” page to find the order you want to modify. Then click create shipping label. Modify the package material and and reprint the shipping label
Note: Precautions for regenerating the shipping label.
If a shipping label is generated for this outbound order but the outbound order status is not “Complete”, you can still replace the shipping label.
However, if the shipping cost for this order has already been billed before WMS replaces the shipping label, there will be a new shipping cost generated, and the previous shipping label will be canceled.The cost of the warehouse will be updated, but there won’t be any changes at shipping cost for OMS, it’s still the original one.
The right thing to do in order to get the correct shipping cost is to remove the previous transactions from the bill first, then replace the replace or recreate the label (If the bill is not paid yet)
Note: Packaging material matching logic
1.When the product of the outbound order is “Ready to Ship”, no matter how many products are sent at a time, the system will not match the packaging materials:
When the outbound product=1, use the size and weight of the product itself to calculate the shipping fee;
When the outbound product>1, the total volume of the outbound order will be automatically calculated by the system for a minimum order volume (system algorithm: add the product volume to get the total volume, the longest side of all products is taken as the length. Volume sum/L=ms, W and H is obtained by taking the square root of ms) the order weight is the sum of the weight of all products in the outbound order;
2.When the product of the outbound order is “package needed”, the warehouse needs to select the specified packaging material for this SKU. If it is not set, the system will not automatically match the packaging material.
If the warehouse specifies a packaging material, it will only be applied when there is only one product. If the shipped product is ≥2, the system will not automatically match the packaging material.
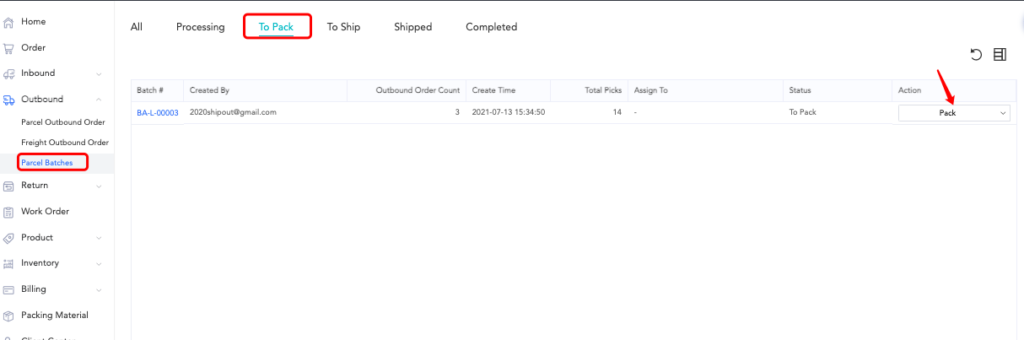
4.Bulk delivery
After packing phase, enter the “To Ship” page, go to the drop-down menu > click “Ship” to complete the shipment;
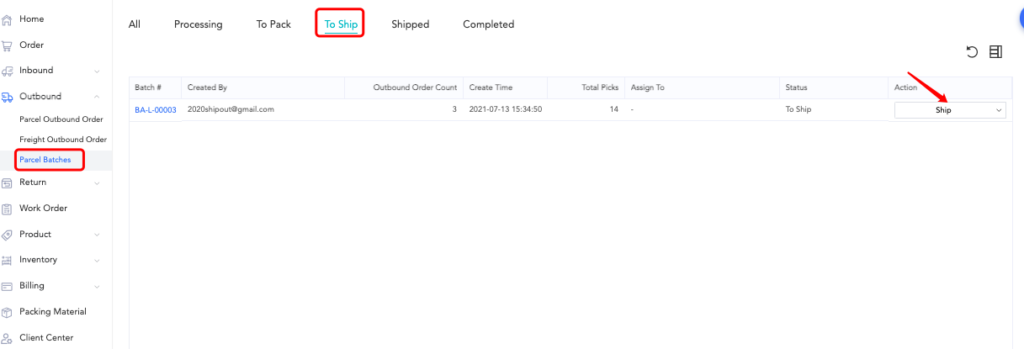
After the order is shipped go to the “Shipped” interface, and you can confirm the cost of this batch of orders;
Steps: Shipped> Complete>Check each charge>Confirm, if the charge needs to be adjusted, click drop-down then”Edit”> Create a new billing item as needed or delete an incorrect billing item;
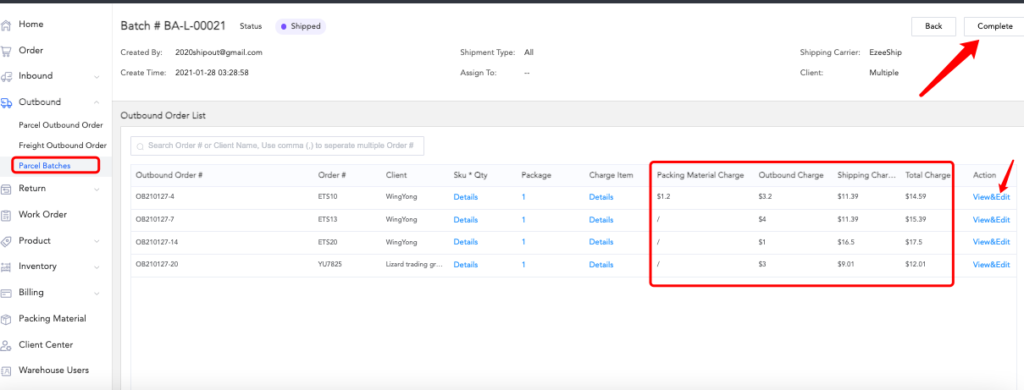